Operational Efficiency Through TPM
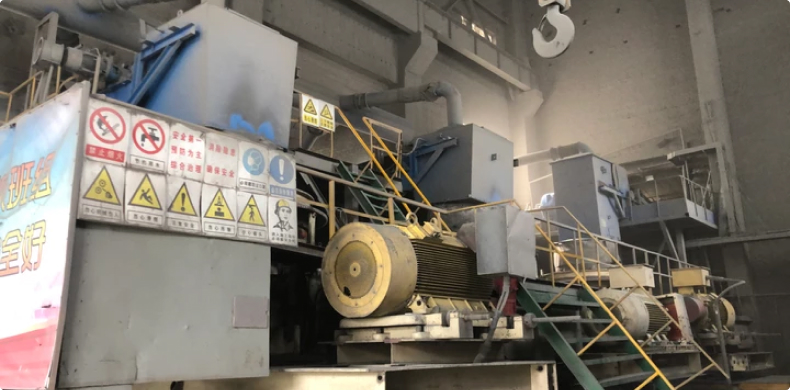
Mining equipment availability is critical to its operational efficiency. In September 2020, the company introduced a new asset management system based on TnPM (Total “normalized” Productive Maintenance), a version of Total Productive Maintenance (TPM) popularized in China.
As a method of physical asset management, the objective of a TPM strategy is to improve the overall availability of equipment and machinery through proactive and preventive asset maintenance.
Complex Operations
The extraction of iron ore and its transformation involve complex workflows and various production equipment and machinery.
Iron ore is an essential raw material used in the production of steel. Its extraction and transformation involve several processes such as crushing, grinding, magnetic separation, flotation, and gravity separation. The Company also provides iron pellets, mainly used for blast furnace ironmaking, and iron powder, a concentrate of iron ore used for iron and steel smelting.
The equipment and machinery in use are spread out over vast areas: The company’s Inner Mongolia operations cover an area of 20 square kilometers, equivalent to a third of Manhattan. The site comprises four mines and represents an annual ore extraction volume of 1.8 million tons. Adding to the overall complexity are operational conditions typical of mining sites: 900 people at an isolated location, operating 24/7 in shifts, at depths of up to 900 meters.
Safety and Operational Requirements
Dazhong Mining requires one comprehensive inventory per year covering all mining assets. All production equipment is checked quarterly, while some critical safety equipment is inspected daily.
The sheer size and scale of the site made manual inventories difficult and time-consuming, with the yearly inventory taking about two months to complete.
The team would carry thick paper inventory lists, check each asset one by one, start on the surface, and proceed underground. A technician would update each record on paper before inputting the data manually in the company’s system, leading to repeated human errors and information losses.
The company realized that its objective of TPM would require a new approach for the efficient and accurate management of its assets.
Data for CMMS
Dazhong Mining was looking for an RFID System to provide data for its Computerized Maintenance Management System (CMMS), and Xerafy recommended the Cargo TRAK.
Xerafy offered its Cargo TRAK, a tag from the OUTDOOR series of long-range RFID tags for inventory tracking.
The Xerafy Cargo TRAK is part of the OUTDOOR series of Industrial RFID tags designed for operations in the field. Each UHF RFID tag comes with its unique identification number, and with an IP68 case and read range of 12 meters (6 meters off-metal), it is a strong choice for asset tracking in the field above and below ground.
The tag’s ability to be used on metal and non-metal surfaces provides a universal tagging solution that suits any mining equipment and machinery. The tag’s rivet holes allow for strong fastening, with adhesive and cable tie options available as well.
Tracking Assets In The Field
“It used to take two weeks to locate, identify, and record all information for 272 assets in the field. With our RFID System, we need less than one week, a 50% time-saving, with full data accuracy.”, Mr. Tian, Equipment Manager.
Inventories in the field are now conducted using an RFID-enabled mobile PDA. The inventory application runs on the device, which allows for data capture at a distance, in bulk, even in poor visibility.
With the asset management solution deployed at both its Inner Mongolia and Anhui mining sites, Dazhong Mining is looking beyond production equipment to include fixed assets and office equipment management and further drive its operational efficiency.